Resources | All Resources
WearCheck Knowledge & Expertise
WearCheck has the benefit of a global network of industry knowledge leaders. The following resources are drawn from hundreds of years of their experience in the oil analysis industry. We hope you find these resources helpful in your understanding of oil analysis and provide you with an oil analysis program of increased value.
All Resources
Measuring and Treating Varnish Formation in Turbine Oils
In this Technical Bulletin we discuss the treatment of varnish deposits in turbine oil, control valves and other machinery parts. We also look at what information can be gleaned from the varnish deposits, and how the data can be used to optimise turbine uptime and reduce maintenance costs. Laboratory test methods have now been developed to measure the varnish potential of turbine oils. The test method is colorimetric – it measures the total colour intensity of a patch to determine the varnish potential of the oil. It also can determine certain colour components of the patch which can help to pin-point the stress mode taking place in the oil that is leading to varnish formation.
SOS : Sources of Silicon
Oil analysis is a well-established condition monitoring technique that has been with us since the late 1940s. It originally developed from a need to monitor main bearing wear in locomotive engines in the United States by spectrometrically measuring the amount of lead in the engine oil. Oil analysis has come a very long way in the last 60 years with the introduction of a whole range of tests that include acid and base numbers, particle counting, infra-red spectroscopy, viscosity, water and fuel contamination and many, many more. However, spectrometric analysis still remains at the core of any oil analysis programme and provides the greatest amount of information in the shortest possible time and at the lowest cost.
Liquid Chromatography and it`s Application in Transformer Oil Analysis
The laboratories of condition monitoring specialists WearCheck are equipped to monitor oil and fluids from a wide array of industrial machinery, including transformer oil, utilising a number of sophisticated analytical techniques, one of which is the focus of this Technical Bulletin. Before I get into the liquid chromatography technique, I would like to briefly cover what it is we would use this technique for, and why.
Solids, Liquids and Gases
In this bulletin we discuss solids, liquids and gases and how they relate to dirt, water and air – three of the most common contaminants found in oil. We look at what they are, what causes them, what damage they do, how we detect them and how to prevent them from causing problems.
Dirty Diesel
Although not an issue in terms of contamination, sulphur is an area of concern. There is a range of valid reasons for the removal of sulphur from our diesel supplies. The first most pressing reason is that high sulphur diesels produce sulphur oxides on combustion which, when dissolved in the other by-product of combustion – water - form strong acids. When these acids condense they attack the metal surfaces of valve guides, cylinder liners and bearings. The acids produced are neutralised by the engine lubricant and, in doing so, reduce the working life of the lubricant necessitating shorter drain intervals.
We are ready for more soot
Get Ready for More Soot’ is the title of an article written by Drew Troyer of the Noria Corporation for publication in Practising Oil Analysis. It deals in part with the effect that current and proposed environmental legislation would have on the performance of engine lubricants. This Technical Bulletin takes a close look at soot, why it is a problem, why is it becoming more of a problem and how to measure its presence in oil.
Detecting Particles in Oil (Part 1)
In simple terms, monitoring wear particles in used oil samples from plant and equipment enables specialists to decide whether they are normal or abnormal and what the likely consequences will be for the machine. In real terms, this is a fairly complicated process. This technical bulletin outlines some of the techniques used in Wearcheck"s oil analysis laboratories to detect and quantify particle contamination, and discusses the value and limitations of these methods in detecting abnormal wear situations.
Detecting Particles in Oil (Part 2)
In the last technical bulletin we looked at four of the seven techniques used in Wearcheck"s oil analysis laboratories to detect and quantify particle contamination, as well as the value and limitations of these methods in detecting abnormal wear situations. In this issue we examine the remaining three techniques.
Sludge
Sludge (noun) : Thick, greasy mud; sewage; muddy or slushy sediment or deposit; accumulation of dirty oil, esp. in sump of internal combustion engine. This is how the Oxford English Dictionary defines sludge and it is a very accurate description of what is found in the sumps of internal combustion engines. In this case, sludge is a collection of resins, lacquers, combustion by-products, oil degradation by-products, water, dirt and wear metals. However, to the tribologist and the mechanical engineer there is a more specific definition for the word sludge: fuel soot, a combustion by-product. This can lead to come confusion as the two definitions are frequently used interchangeably.
Silicon....enemy number one
After oxygen, silicon is the most abundant element in the earth"s crust. Silicon does not occur naturally in elemental form but rather combined with oxygen in a compound called silica (silicon dioxide). Silica occurs in a free form (quartz, sand, etc.) or combined with a variety of metallic oxides, in which case it is called a silicate (eg. Felspar). Another class of silicon compounds that should not be confused with silica and silicates is silicones. Silicones are man-made organic compounds that find extensive application in the polish, paint and lubrication industries.
Particle Counting and Contamination Analysis in Fluid Power Systems
Typically most oil analysis companies have relied on spectrometric and debris analysis for the detection of wear particles and contaminants in the oil lubricated components. The ICP (inductively coupled plasm) spectrometer used by WearCheck is limited to a maximum particle size of eight microns that it can detect, so other techniques must be employed to detect larger wear particles and contaminants. The ideal situation would be to filter all oil samples and examine any debris under a microscope; this is highly labour intensive in terms of sample preparation and visual analysis of the debris and only provides a qualitative description of the debris.
All Resources Categories
Resource Categories
In this Technical Bulletin we discuss the treatment of varnish deposits in turbine oil, control valves and other machinery parts. We also look at what information can be gleaned from the varnish deposits, and how the data can be used to optimise turbine uptime and reduce maintenance costs. Laboratory test methods have now been developed to measure the varnish potential of turbine oils. The test method is colorimetric – it measures the total colour intensity of a patch to determine the varnish potential of the oil. It also can determine certain colour components of the patch which can help to pin-point the stress mode taking place in the oil that is leading to varnish formation.
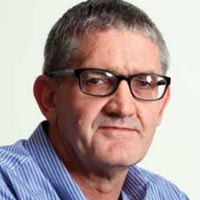
Daan Burger
WearCheck Africa
Oil analysis is a well-established condition monitoring technique that has been with us since the late 1940s. It originally developed from a need to monitor main bearing wear in locomotive engines in the United States by spectrometrically measuring the amount of lead in the engine oil. Oil analysis has come a very long way in the last 60 years with the introduction of a whole range of tests that include acid and base numbers, particle counting, infra-red spectroscopy, viscosity, water and fuel contamination and many, many more. However, spectrometric analysis still remains at the core of any oil analysis programme and provides the greatest amount of information in the shortest possible time and at the lowest cost.
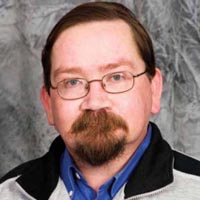
John Evans
WearCheck Africa
The laboratories of condition monitoring specialists WearCheck are equipped to monitor oil and fluids from a wide array of industrial machinery, including transformer oil, utilising a number of sophisticated analytical techniques, one of which is the focus of this Technical Bulletin. Before I get into the liquid chromatography technique, I would like to briefly cover what it is we would use this technique for, and why.
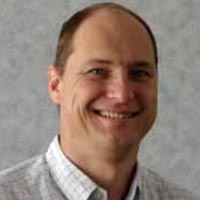
Neil Robinson
WearCheck Africa
In this bulletin we discuss solids, liquids and gases and how they relate to dirt, water and air – three of the most common contaminants found in oil. We look at what they are, what causes them, what damage they do, how we detect them and how to prevent them from causing problems.
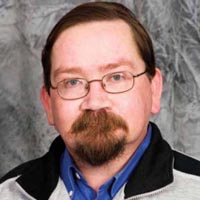
John Evans
WearCheck Africa
Although not an issue in terms of contamination, sulphur is an area of concern. There is a range of valid reasons for the removal of sulphur from our diesel supplies. The first most pressing reason is that high sulphur diesels produce sulphur oxides on combustion which, when dissolved in the other by-product of combustion – water - form strong acids. When these acids condense they attack the metal surfaces of valve guides, cylinder liners and bearings. The acids produced are neutralised by the engine lubricant and, in doing so, reduce the working life of the lubricant necessitating shorter drain intervals.
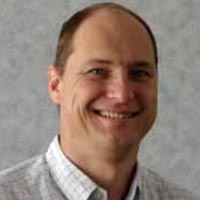
Neil Robinson
WearCheck Africa
Get Ready for More Soot’ is the title of an article written by Drew Troyer of the Noria Corporation for publication in Practising Oil Analysis. It deals in part with the effect that current and proposed environmental legislation would have on the performance of engine lubricants. This Technical Bulletin takes a close look at soot, why it is a problem, why is it becoming more of a problem and how to measure its presence in oil.
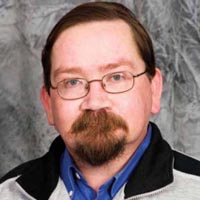
John Evans
WearCheck Africa
In simple terms, monitoring wear particles in used oil samples from plant and equipment enables specialists to decide whether they are normal or abnormal and what the likely consequences will be for the machine. In real terms, this is a fairly complicated process. This technical bulletin outlines some of the techniques used in Wearcheck"s oil analysis laboratories to detect and quantify particle contamination, and discusses the value and limitations of these methods in detecting abnormal wear situations.
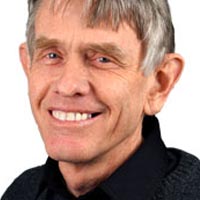
Alistair Geach
WearCheck Canada
In the last technical bulletin we looked at four of the seven techniques used in Wearcheck"s oil analysis laboratories to detect and quantify particle contamination, as well as the value and limitations of these methods in detecting abnormal wear situations. In this issue we examine the remaining three techniques.
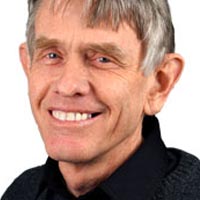
Alistair Geach
WearCheck Canada
Sludge (noun) : Thick, greasy mud; sewage; muddy or slushy sediment or deposit; accumulation of dirty oil, esp. in sump of internal combustion engine. This is how the Oxford English Dictionary defines sludge and it is a very accurate description of what is found in the sumps of internal combustion engines. In this case, sludge is a collection of resins, lacquers, combustion by-products, oil degradation by-products, water, dirt and wear metals. However, to the tribologist and the mechanical engineer there is a more specific definition for the word sludge: fuel soot, a combustion by-product. This can lead to come confusion as the two definitions are frequently used interchangeably.
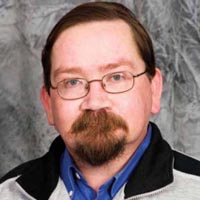
John Evans
WearCheck Africa
After oxygen, silicon is the most abundant element in the earth"s crust. Silicon does not occur naturally in elemental form but rather combined with oxygen in a compound called silica (silicon dioxide). Silica occurs in a free form (quartz, sand, etc.) or combined with a variety of metallic oxides, in which case it is called a silicate (eg. Felspar). Another class of silicon compounds that should not be confused with silica and silicates is silicones. Silicones are man-made organic compounds that find extensive application in the polish, paint and lubrication industries.

Gary Blevins
WearCheck Africa
Typically most oil analysis companies have relied on spectrometric and debris analysis for the detection of wear particles and contaminants in the oil lubricated components. The ICP (inductively coupled plasm) spectrometer used by WearCheck is limited to a maximum particle size of eight microns that it can detect, so other techniques must be employed to detect larger wear particles and contaminants. The ideal situation would be to filter all oil samples and examine any debris under a microscope; this is highly labour intensive in terms of sample preparation and visual analysis of the debris and only provides a qualitative description of the debris.
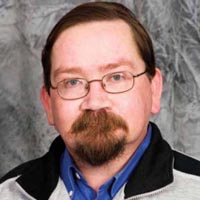