Resources | Technical Documents
WearCheck Knowledge & Expertise
WearCheck has the benefit of a global network of industry knowledge leaders. The following resources are drawn from hundreds of years of their experience in the oil analysis industry. We hope you find these resources helpful in your understanding of oil analysis and provide you with an oil analysis program of increased value.
Technical Documents
Integrate Oil Analysis With Machine Data
Inflation and long lead times for new equipment are among the financial pressures pressing down on fleet managers to extend machine life. Pushing a machine too far results in loss of availability and utilization. A tried-and-true tool for machine health, oil analysis, has evolved with the advent of telematics to interact with machine data in a way that makes these decisions not only easier but also increases the odds that they will be successful. As a service, oil analysis has adapted to the new digital world to continue to provide value to the fleet asset manager. It is no longer enough to provide a web portal to manage oil analysis programs and view sample reports. Equipment-using organizations are expecting a tighter level of machine-data integration to drive higher levels of efficiency in all aspects of their business, and fleet maintenance is no exception.
Why Maintenance Planning and Scheduling may Fail (Part 2)
In this article, we discuss the six principles of maintenance scheduling and their importance to the maintenance function. Scheduling is sort of a direct response to Parkin’s Law (1955), which states that the amount of work assigned expands to fill the amount of time available. Visualise waking up without a to-do list on your day off from work - you might be able to do one or two tasks that day, but when you wake up with a list of five tasks, you might accomplish three or four of them. You might not be able to accomplish all five tasks on your list, but being able to complete three or four of them is far more of an achievement than just waking up without a plan and seeing how the day proceeds. Scheduling is all about goal setting, which involves giving enough work to craft crews to fill up a forecast of crew-work hours available - whether for a day or a week.
Why Maintenance Planning and Scheduling may Fail (Part 1)
This article discusses what causes maintenance planning and scheduling to fail to increase maintenance productivity, when at a casual glance, the framework of planning and scheduling seems to be in place in most industrial plants. The planning function and the scheduling function each have six principles, which, when applied in their correct sequence, ensure that the maintenance planning and scheduling process will be able to deliver its main objective – to increase maintenance productivity. The article starts with a discussion of the six principles of maintenance planning.
Dipstick Disasters and Loss Control
Say ‘dipstick’ and any driver’s mind flies towards an engine oil dipstick – especially older truck models that are not electronically equipped with sumplevel sensors and instrument panel signals. But modern trucks come standard with other fluid dipsticks as well, and that is where it all begins. A driver’s daily check sheet will include engine oil levels. But, unless the check is specific and limited to the engine only with training on how and when to read the dipstick, there is a danger that an ‘enthusiastic’ driver starts checking all the other dipstick levels that are best left to workshop technicians. Power steering, torque convertor automatic transmissions, and automated manual transmission (AMT) viscous couplings all require top-up techniques at operating temperatures with absolute cleanliness. Also, some systems - such as automatic gearboxes - require the lubricant level to be checked while the engine is running at idle.
Talking Transformer Testing
Condition monitoring is the frequent collecting, measuring, recording, and analysis of the relevant data regarding an asset’s operation. If we interpret the data correctly, it can give us great insight into the asset’s condition. Frequent monitoring of the asset can result in less maintenance required or more extended periods without any maintenance required. It is crucial to identify the key parameters that are needed to give us a complete picture of the actual status of the transformer and the action we need to take to ensure the continued reliability of the asset to achieve the maximum lifetime.
The Future of Oil Analysis: Converting to Electric Power and Sensors
This article is from the STLE's TLT magazine, with contributions from Bill Quesnel of WearCheck Canada. With new technologies on the horizon, watching the oil analysis industry and planning for the future are key. Commercial oil analysis laboratories play a key role in the oil condition monitoring industry, but sensor technology and electrification have the potential to disrupt the status quo. Oil sensor technology is expanding, but high costs and low buy-in have prevented it from significantly displacing the role oil analysis laboratories play in the oil condition monitoring industry. Electrification, especially in the trucking industry, has a high potential to disrupt the oil condition monitoring industry because many commercial oil analysis laboratories focus on diesel engine testing.
Idling - Costly Fuel, Wear, and Engine-life Thief
Excessive idling is one of the most counter-productive facets of running a fleet of vehicles. In this Technical Bulletin, trucking expert Dave Scott discusses the effects of excessive idling and how to avoid it to minimise the negative consequences.
A New Perspective on Modern Day Maintenance (Part 2)
In this edition, I outline what several renowned maintenance practitioners believe is the best way to transition an organisation’s maintenance philosophy. Fundamentally, we do maintenance to achieve reliability, and, according to well-known author Ron Moore, ‘A reliable plant is a safe plant, is a profitable plant’. Profitability of any industrial plant is directly linked to its reliability, which in turn is determined by the quality of maintenance practiced. If we don’t maintain our assets, things can go terribly wrong. Almost all industrial disasters had poor maintenance reliability practices as one of the contributing causes.
A New Perspective on Modern Day Maintenance
WearCheck provides thousands of customers each year with world-class condition monitoring (CM) services, which have been proven time and again to save time and money for companies by identifying potential machine failure before it happens and remedying the problem. However, in our line of work as condition monitoring (CM) specialists, we still do come across customers who have everything to gain by using the CM techniques we offer but, unfortunately, they don’t see the benefits to be gained. No matter how hard we try to convince them, they stubbornly continue to refuse help.
Diesel Emissions : A Breath of Fresh Air (Part 2)
We continue our discussion around reducing air pollution through stricter diesel engine emission standards and techniques. In this Technical Bulletin - the second of a two part series – we examine the intricacies of appropriate lubricant viscosity as well as the performance criteria of a range of additives and how they contribute to the war against harmful emissions, or not.
Diesel Emissions : A Breath of Fresh Air
As the world moves to adopt more planet-friendly strategies, air pollution is a key focus area for engine-manufacturers and operators. In this technical bulletin - the first of a two part series - global diesel engine emission standards are discussed, along with a range of techniques that reduce emissions, which ones are most effective, and why.
Navigating the Online Vibration Analysis Minefield
There is currently a notable spike in online installations in all industries, driven by Industry 4.0. This trend is also evident in the condit ion monitoring field. Installing online vibration transducers is a revolutionary step in the monitoring process but can be challenging without knowing what is available in the market and without a comprehensive understanding of the equipment capabilities and the relevant terminology. In this Technical Bulleting, we will guide you through the minefiled of available technology, discussing the different measuring capacities, installation levels and how these can be aligned with your requirements.
The Engine Killers
I have a colleague who believes that engines don’t just simply die, they are murdered. A rather dramatic sentiment, I know, but then we take the death of an engine quite seriously at WearCheck. Being an avid consumer of forensics crime drama television series like CSI (Crime Scene Investigation) I feel that I can confidently explain the procedure that takes place once a murder victim has come to the attention of the authorities.
Reliability, Procurement and Spares Management
Effective asset optimisation plays a key rôle in boosting reliability as well as the efficient management of maintenance costs in any given operation. This Technical Bulletin discusses various scenarios in which maintenance costs can be reduced through improved procurement systems and better management of spares.
Keep it Clean
In today’s highly competitive global economy, the concept of machine reliability has led many an organisation to make the paradigm shift to proactive maintenance practices that take a holistic approach to asset management and contamination control. This focus on asset management and contamination control has highlighted the important rôle lubricants play in achieving machine reliability. Lubricants are no longer seen as merely consumables, but rather an integral part of a mechanical system having just as much merit as the componentry they lubricate and protect.
Condition-Based Assessment of On-Load Tap Changers
On-load tap changers (OLTCs) are a crucial element of utility networks, as they must operate in a precise fashion in order to maintain a constant voltage output. This must be achieved regardless of variation on input or load. OLTCs have been a weak link in many networks, as they deteriorate over time due to mechanical problems or contact wear from repeated operation. Erosion of the contacts over time is expected due to the nature of their function. Coking of the contacts causes overheating, which can cause thermal runaway. Regular maintenance is necessary to ensure continued proper functioning.
Elimination of Poisonous PCB Contamination in Electrical Equipment
PCB (polychlorinated biphenyl) is a highly toxic combination of molecules, which first came into existence in the late 1800s. The prevalence of PCBs mushroomed in the late 1920s as the technical benefits of the chemical compound were recognised and developed. Present day scientists, governments and businesses are tasked with eliminating PCBs as much as possible, due to their harmful, carcinogenic properties.
CH4 can be Worth so much More (Part 1)
It is said that energy is the blood that runs through the veins of every economy. It is to the survival of an economy what water is to the survival of the human body. Without energy, the wheels of the economy literally do not turn. Energy is consequently a facilitator of economic development and stability. According to the South African department of energy (DoE), energy security within the South African context means ensuring that diverse energy resources, in sustainable quantities and at affordable prices, are available to the South African economy in support of economic development and poverty alleviation, taking into account environmental management requirements.
CH4 can be Worth so much More (Part 2)
In this final instalment, we will look at what oil analysis can measure in terms of the third function of oil analysis, which is to detect oil degradation. Oil is the lifeblood of any mechanical system and as such has many functions to perform. These functions can be categorised into four fundamental groups: reduction of wear, removal of contaminants, removal of heat and acting as a structural material. All these functions are negatively impacted if the oil physically or chemically degrades.
Using Oil Analysis to Monitor Your Lubrication Management Program
There is no question that an effective oil analysis program lowers maintenance costs on rotating equipment. The trick is knowing how to run an effective oil analysis program. Companies must be proactive, so that the solution to an oil-related problem is not always an oil change. The real benefit of oil analysis is using the data to steer you towards solutions to eliminate oil issues. Typical Internal Rates of Return (IRR) and Net Present Value over five years (NPV) for a lubrication management program in a medium sized plant are about 150% and $500,000. In this article, I will provide you with best practices for using oil analysis to monitor your lubrication management program.
World-Class Lubrication Management for Gearboxes
As the saying goes, "an ounce of prevention is worth a pound of cure." When it comes to maintenance of your plant's gearboxes, this is definitely true. By using an industry-leading Lubrigard gearbox adapter kit to perform regular maintenance, a company will save money and time, reduce operating costs and have longer-lasting, more reliable equipment. For an average $600 investment, a company can protect an $80,000 piece of equipment.
Oil - An Asset, Not a Consumable
The days of "oil is oil" have long gone. It is vitally important that in this day and age, oil needs to be considered as an asset rather than just a consumable, and as an asset, it needs to be managed. This brief paper will take a look at how oils are selected and then managed throughout the plant as a valuable asset like any other piece of industrial equipment.
The Low-down on Lower Emissions array(Part 1)
The automotive industry in South Africa is largely focused at the moment on lowering vehicle exhaust emissions. This follows a global movement towards more stringent air emission control laws in man’s attempt to slow down the destruction of our planet through global warming. So what is all the hype about? A basic understanding of the fundamentals of global warming in terms of the greenhouse effect is needed in order to understand the advances the automotive industry is implementing to combat dangerous exhaust emissions.
The Low-down on Lower Emissions array(Part 2)
It was seen in the last Technical Bulletin that, in order to reduce our effect on the environment due to harmful vehicular exhaust emissions, we need to ensure a reduction of the emissions. This is now reality due to the new laws being implemented around the world. So what is being done to ensure this happens and what part do we, as the consumer and concerned citizen, play in all this?
Clean Oil Saves Money
In our current economic age, companies are forced to pursue every avenue for cost saving to ensure that their chance of financial success is maximised. Lubricated mechanical equipment is a significant cost to many companies and, through careful management, significant savings can be achieved. This technical bulletin looks at particle counting, explains the jargon and technology, and shows you how by monitoring your oil’s cleanliness you can reduce repairs, maintenance costs and downtime and save on your bottom line.
How to calculate the effect Oil Analysis has on the Bottom Line
Over the last ten years there has been a paradigm shift that has seen maintenance become almost synonymous with achieving reliability. Let"s start by looking at a few definitions.
The humble sub-form is the linchpin of oil analysis array(Part 1)
In countless articles, seminars, training courses and technical bulletins it has been stressed that there are two main reasons for an oil analysis programme to fail. The first is that the oil sample is not representative of the oil in the system, in other words, the dreaded ‘bad sample’. The second involves information regarding the sample. This can either be wrong or, quite simply, missing. In the majority of cases it is the second reason that causes the most problems, not just in terms of the diagnosis but for data processing and the laboratory.
The humble sub-form is the linchpin of oil analysis array(Part 2)
This is the second part of the article on how to submit a submission form and what can go wrong if any information is missing or incorrect. This is vitally important considering that 20% of all samples are submitted to Wearcheck with incorrect or insufficient details, causing costly delays and hampering accurate diagnosis. An example of a submission form appears on page 3.
Keep your cool array(Managing Cooling Systems)
During operation, all internal combustion engines produce heat as a by-product of combustion. The temperature of burning fuel can reach 2000°C. However, only about 33% of this is transferred into power through the crankshaft. Approximately 30% is expelled through the exhaust whilst another 7% or so is lost through radiation. The remaining 30% must be dissipated through a cooling system. In addition to removing heat from burnt fuel, the cooling system also removes heat from other sources such as turbochargers, torque converters and hydraulic or transmission oil coolers.
The Perils, Pitfalls and Perks of extending oil drain periods
The extension of oil drain periods has long been an area of debate. There are many benefits to be obtained from extending oil drain periods and doing so is a legal requirement in certain countries around the world. These benefits are just as applicable to South Africa but it would be foolish to try to apply parameters recommended for European, Japanese or North American conditions (the source of most diesel engine technology) to this country.
Clean up your act
It is widely accepted that oil contamination is the one of the major causes of component failure. When practising proactive maintenance it therefore makes sense to give oil cleanliness a high priority. This technical bulletin will deal primarily with particulate contamination, the causes, and how to avoid it. By maintaining a high level of oil cleanliness, machinery failure, resultant downtime and expensive repair costs can be kept to a minimum.
Implementing Reliability-Centered Maintenance (RCM)
Using RCM to develop an initial maintenance program for new equipment as well as scheduled maintenance for existing plant, involves a structured decision-making process based on the consequences of functional failure of this equipment. RCM analysis produces a program which includes all scheduled tasks - and only those tasks - necessary to ensure safety and operating economy. The decision-making logic behind RCM analysis applies to any complex equipment which requires a maintenance support program aimed at maximizing operating reliability at the lowest cost.
Condition-Monitoring, Oil Analysis & More
In this day and age, predictive maintenance and condition monitoring are necessities for any company that has machinery which is critical in achieving production goals. Oil analysis is a condition monitoring technique that has been in use for more than 50 years and has proved to be a highly effective management tool for monitoring the health of lubricated machinery and the lubricants themselves. However, oil analysis is not the only condition monitoring technique available to today"s maintenance professional. Other techniques such as vibration monitoring, thermography and ultra-sonic analysis can also be used. This Technical Bulletin will look at the evolution of maintenance philosophies, the goals of a condition monitoring programme and how a combination of different analytical practices can be used to achieve these goals.
Reliability-Centered Maintenance
Maintenance philosophies and practices have been around for many years - the objective of these philosophies being the economic consideration of optimizing plant availability in industry. There has been a steady evolution from breakdown maintenance to predictive maintenance to proactive maintenance in the quest to keep industrial equipment operating economically, efficiently and safely.
Technical Documents Categories
Resource Categories
Inflation and long lead times for new equipment are among the financial pressures pressing down on fleet managers to extend machine life. Pushing a machine too far results in loss of availability and utilization. A tried-and-true tool for machine health, oil analysis, has evolved with the advent of telematics to interact with machine data in a way that makes these decisions not only easier but also increases the odds that they will be successful. As a service, oil analysis has adapted to the new digital world to continue to provide value to the fleet asset manager. It is no longer enough to provide a web portal to manage oil analysis programs and view sample reports. Equipment-using organizations are expecting a tighter level of machine-data integration to drive higher levels of efficiency in all aspects of their business, and fleet maintenance is no exception.
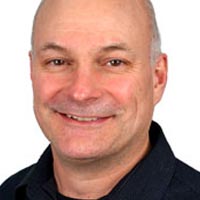
Bill Quesnel
WearCheck Canada
In this article, we discuss the six principles of maintenance scheduling and their importance to the maintenance function. Scheduling is sort of a direct response to Parkin’s Law (1955), which states that the amount of work assigned expands to fill the amount of time available. Visualise waking up without a to-do list on your day off from work - you might be able to do one or two tasks that day, but when you wake up with a list of five tasks, you might accomplish three or four of them. You might not be able to accomplish all five tasks on your list, but being able to complete three or four of them is far more of an achievement than just waking up without a plan and seeing how the day proceeds. Scheduling is all about goal setting, which involves giving enough work to craft crews to fill up a forecast of crew-work hours available - whether for a day or a week.
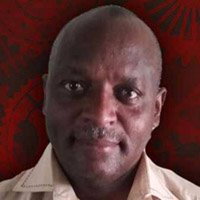
Raymond Chizu
WearCheck Africa
This article discusses what causes maintenance planning and scheduling to fail to increase maintenance productivity, when at a casual glance, the framework of planning and scheduling seems to be in place in most industrial plants. The planning function and the scheduling function each have six principles, which, when applied in their correct sequence, ensure that the maintenance planning and scheduling process will be able to deliver its main objective – to increase maintenance productivity. The article starts with a discussion of the six principles of maintenance planning.
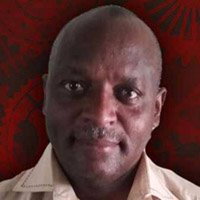
Raymond Chizu
WearCheck Africa
Say ‘dipstick’ and any driver’s mind flies towards an engine oil dipstick – especially older truck models that are not electronically equipped with sumplevel sensors and instrument panel signals. But modern trucks come standard with other fluid dipsticks as well, and that is where it all begins. A driver’s daily check sheet will include engine oil levels. But, unless the check is specific and limited to the engine only with training on how and when to read the dipstick, there is a danger that an ‘enthusiastic’ driver starts checking all the other dipstick levels that are best left to workshop technicians. Power steering, torque convertor automatic transmissions, and automated manual transmission (AMT) viscous couplings all require top-up techniques at operating temperatures with absolute cleanliness. Also, some systems - such as automatic gearboxes - require the lubricant level to be checked while the engine is running at idle.
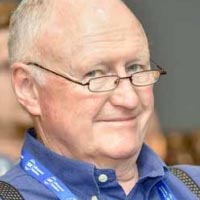
Dave Scott
WearCheck Afrcia
Condition monitoring is the frequent collecting, measuring, recording, and analysis of the relevant data regarding an asset’s operation. If we interpret the data correctly, it can give us great insight into the asset’s condition. Frequent monitoring of the asset can result in less maintenance required or more extended periods without any maintenance required. It is crucial to identify the key parameters that are needed to give us a complete picture of the actual status of the transformer and the action we need to take to ensure the continued reliability of the asset to achieve the maximum lifetime.
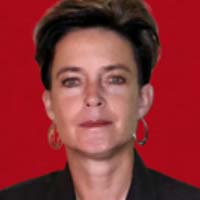
Corné Dames
WearCheck Africa
This article is from the STLE's TLT magazine, with contributions from Bill Quesnel of WearCheck Canada. With new technologies on the horizon, watching the oil analysis industry and planning for the future are key. Commercial oil analysis laboratories play a key role in the oil condition monitoring industry, but sensor technology and electrification have the potential to disrupt the status quo. Oil sensor technology is expanding, but high costs and low buy-in have prevented it from significantly displacing the role oil analysis laboratories play in the oil condition monitoring industry. Electrification, especially in the trucking industry, has a high potential to disrupt the oil condition monitoring industry because many commercial oil analysis laboratories focus on diesel engine testing.
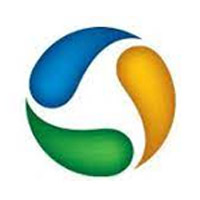
STLE
WearCheck Canada
Excessive idling is one of the most counter-productive facets of running a fleet of vehicles. In this Technical Bulletin, trucking expert Dave Scott discusses the effects of excessive idling and how to avoid it to minimise the negative consequences.
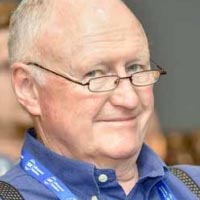
Dave Scott
WearCheck Africa
In this edition, I outline what several renowned maintenance practitioners believe is the best way to transition an organisation’s maintenance philosophy. Fundamentally, we do maintenance to achieve reliability, and, according to well-known author Ron Moore, ‘A reliable plant is a safe plant, is a profitable plant’. Profitability of any industrial plant is directly linked to its reliability, which in turn is determined by the quality of maintenance practiced. If we don’t maintain our assets, things can go terribly wrong. Almost all industrial disasters had poor maintenance reliability practices as one of the contributing causes.
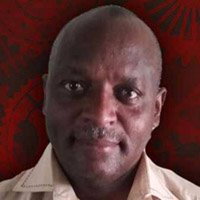
Raymond Chizu
WearCheck Africa
WearCheck provides thousands of customers each year with world-class condition monitoring (CM) services, which have been proven time and again to save time and money for companies by identifying potential machine failure before it happens and remedying the problem. However, in our line of work as condition monitoring (CM) specialists, we still do come across customers who have everything to gain by using the CM techniques we offer but, unfortunately, they don’t see the benefits to be gained. No matter how hard we try to convince them, they stubbornly continue to refuse help.
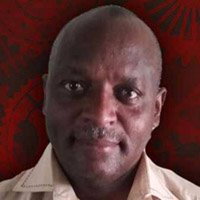
Raymond Chizu
WearCheck Africa
We continue our discussion around reducing air pollution through stricter diesel engine emission standards and techniques. In this Technical Bulletin - the second of a two part series – we examine the intricacies of appropriate lubricant viscosity as well as the performance criteria of a range of additives and how they contribute to the war against harmful emissions, or not.
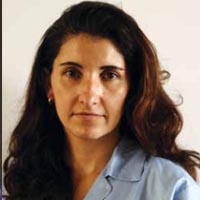
Steven Lara-Lee Lumley
WearCheck Afrcia
As the world moves to adopt more planet-friendly strategies, air pollution is a key focus area for engine-manufacturers and operators. In this technical bulletin - the first of a two part series - global diesel engine emission standards are discussed, along with a range of techniques that reduce emissions, which ones are most effective, and why.
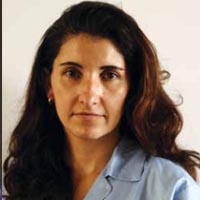
Steven Lara-Lee Lumley
WearCheck Africa
There is currently a notable spike in online installations in all industries, driven by Industry 4.0. This trend is also evident in the condit ion monitoring field. Installing online vibration transducers is a revolutionary step in the monitoring process but can be challenging without knowing what is available in the market and without a comprehensive understanding of the equipment capabilities and the relevant terminology. In this Technical Bulleting, we will guide you through the minefiled of available technology, discussing the different measuring capacities, installation levels and how these can be aligned with your requirements.
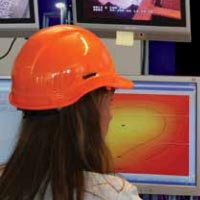
WearCheck Reliability Solutions
WearCheck Africa
I have a colleague who believes that engines don’t just simply die, they are murdered. A rather dramatic sentiment, I know, but then we take the death of an engine quite seriously at WearCheck. Being an avid consumer of forensics crime drama television series like CSI (Crime Scene Investigation) I feel that I can confidently explain the procedure that takes place once a murder victim has come to the attention of the authorities.
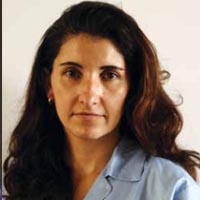
Steven Lara-Lee Lumley
WearCheck Africa
Effective asset optimisation plays a key rôle in boosting reliability as well as the efficient management of maintenance costs in any given operation. This Technical Bulletin discusses various scenarios in which maintenance costs can be reduced through improved procurement systems and better management of spares.
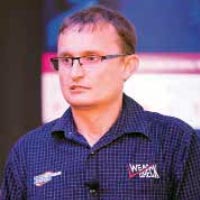
Dennis Swanepoel
WearCheck Africa
In today’s highly competitive global economy, the concept of machine reliability has led many an organisation to make the paradigm shift to proactive maintenance practices that take a holistic approach to asset management and contamination control. This focus on asset management and contamination control has highlighted the important rôle lubricants play in achieving machine reliability. Lubricants are no longer seen as merely consumables, but rather an integral part of a mechanical system having just as much merit as the componentry they lubricate and protect.
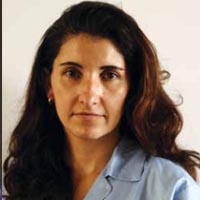
Steven Lara-Lee Lumley
WearCheck Africa
On-load tap changers (OLTCs) are a crucial element of utility networks, as they must operate in a precise fashion in order to maintain a constant voltage output. This must be achieved regardless of variation on input or load. OLTCs have been a weak link in many networks, as they deteriorate over time due to mechanical problems or contact wear from repeated operation. Erosion of the contacts over time is expected due to the nature of their function. Coking of the contacts causes overheating, which can cause thermal runaway. Regular maintenance is necessary to ensure continued proper functioning.
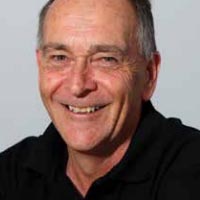
I.A.R. Gray
WearCheck Africa
PCB (polychlorinated biphenyl) is a highly toxic combination of molecules, which first came into existence in the late 1800s. The prevalence of PCBs mushroomed in the late 1920s as the technical benefits of the chemical compound were recognised and developed. Present day scientists, governments and businesses are tasked with eliminating PCBs as much as possible, due to their harmful, carcinogenic properties.
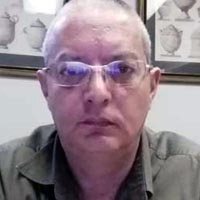
Gert Nel
WearCheck Africa
It is said that energy is the blood that runs through the veins of every economy. It is to the survival of an economy what water is to the survival of the human body. Without energy, the wheels of the economy literally do not turn. Energy is consequently a facilitator of economic development and stability. According to the South African department of energy (DoE), energy security within the South African context means ensuring that diverse energy resources, in sustainable quantities and at affordable prices, are available to the South African economy in support of economic development and poverty alleviation, taking into account environmental management requirements.
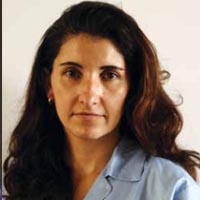
Steven Lara-Lee Lumley
WearCheck Africa
In this final instalment, we will look at what oil analysis can measure in terms of the third function of oil analysis, which is to detect oil degradation. Oil is the lifeblood of any mechanical system and as such has many functions to perform. These functions can be categorised into four fundamental groups: reduction of wear, removal of contaminants, removal of heat and acting as a structural material. All these functions are negatively impacted if the oil physically or chemically degrades.
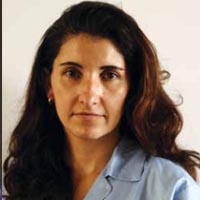
Steven Lara-Lee Lumley
WearCheck Africa
There is no question that an effective oil analysis program lowers maintenance costs on rotating equipment. The trick is knowing how to run an effective oil analysis program. Companies must be proactive, so that the solution to an oil-related problem is not always an oil change. The real benefit of oil analysis is using the data to steer you towards solutions to eliminate oil issues. Typical Internal Rates of Return (IRR) and Net Present Value over five years (NPV) for a lubrication management program in a medium sized plant are about 150% and $500,000. In this article, I will provide you with best practices for using oil analysis to monitor your lubrication management program.
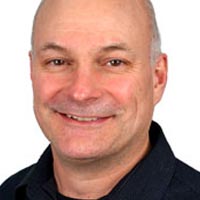
Bill Quesnel
WearCheck Canada
As the saying goes, "an ounce of prevention is worth a pound of cure." When it comes to maintenance of your plant's gearboxes, this is definitely true. By using an industry-leading Lubrigard gearbox adapter kit to perform regular maintenance, a company will save money and time, reduce operating costs and have longer-lasting, more reliable equipment. For an average $600 investment, a company can protect an $80,000 piece of equipment.
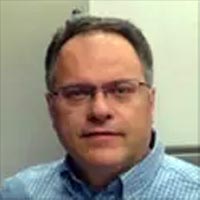
Paul Dumont
WearCheck Canada
The days of "oil is oil" have long gone. It is vitally important that in this day and age, oil needs to be considered as an asset rather than just a consumable, and as an asset, it needs to be managed. This brief paper will take a look at how oils are selected and then managed throughout the plant as a valuable asset like any other piece of industrial equipment.
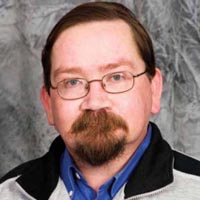
John Evans
WearCheck Africa
The automotive industry in South Africa is largely focused at the moment on lowering vehicle exhaust emissions. This follows a global movement towards more stringent air emission control laws in man’s attempt to slow down the destruction of our planet through global warming. So what is all the hype about? A basic understanding of the fundamentals of global warming in terms of the greenhouse effect is needed in order to understand the advances the automotive industry is implementing to combat dangerous exhaust emissions.
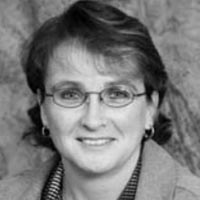
Michelle Allis
WearCheck Africa
It was seen in the last Technical Bulletin that, in order to reduce our effect on the environment due to harmful vehicular exhaust emissions, we need to ensure a reduction of the emissions. This is now reality due to the new laws being implemented around the world. So what is being done to ensure this happens and what part do we, as the consumer and concerned citizen, play in all this?
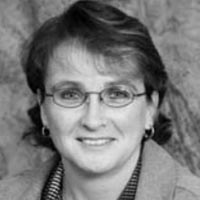
Michelle Allis
WearCheck Africa
In our current economic age, companies are forced to pursue every avenue for cost saving to ensure that their chance of financial success is maximised. Lubricated mechanical equipment is a significant cost to many companies and, through careful management, significant savings can be achieved. This technical bulletin looks at particle counting, explains the jargon and technology, and shows you how by monitoring your oil’s cleanliness you can reduce repairs, maintenance costs and downtime and save on your bottom line.
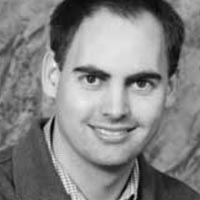
Paul Swan
WearCheck Africa
Over the last ten years there has been a paradigm shift that has seen maintenance become almost synonymous with achieving reliability. Let"s start by looking at a few definitions.
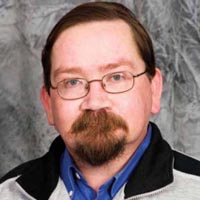
John Evans
WearCheck Africa
In countless articles, seminars, training courses and technical bulletins it has been stressed that there are two main reasons for an oil analysis programme to fail. The first is that the oil sample is not representative of the oil in the system, in other words, the dreaded ‘bad sample’. The second involves information regarding the sample. This can either be wrong or, quite simply, missing. In the majority of cases it is the second reason that causes the most problems, not just in terms of the diagnosis but for data processing and the laboratory.
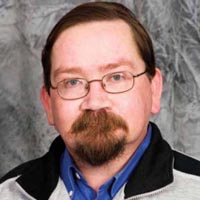
John Evans
WearCheck Africa
This is the second part of the article on how to submit a submission form and what can go wrong if any information is missing or incorrect. This is vitally important considering that 20% of all samples are submitted to Wearcheck with incorrect or insufficient details, causing costly delays and hampering accurate diagnosis. An example of a submission form appears on page 3.
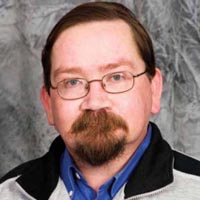
John Evans
WearCheck Africa
During operation, all internal combustion engines produce heat as a by-product of combustion. The temperature of burning fuel can reach 2000°C. However, only about 33% of this is transferred into power through the crankshaft. Approximately 30% is expelled through the exhaust whilst another 7% or so is lost through radiation. The remaining 30% must be dissipated through a cooling system. In addition to removing heat from burnt fuel, the cooling system also removes heat from other sources such as turbochargers, torque converters and hydraulic or transmission oil coolers.
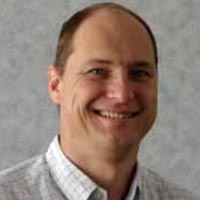
Neil Robinson
WearCheck Africa
The extension of oil drain periods has long been an area of debate. There are many benefits to be obtained from extending oil drain periods and doing so is a legal requirement in certain countries around the world. These benefits are just as applicable to South Africa but it would be foolish to try to apply parameters recommended for European, Japanese or North American conditions (the source of most diesel engine technology) to this country.
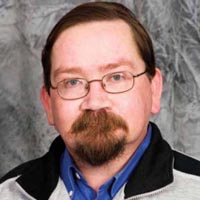
John Evans
WearCheck Africa
It is widely accepted that oil contamination is the one of the major causes of component failure. When practising proactive maintenance it therefore makes sense to give oil cleanliness a high priority. This technical bulletin will deal primarily with particulate contamination, the causes, and how to avoid it. By maintaining a high level of oil cleanliness, machinery failure, resultant downtime and expensive repair costs can be kept to a minimum.
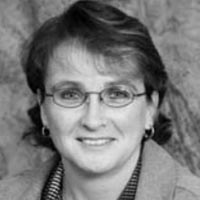
Michelle Allis
WearCheck Africa
Using RCM to develop an initial maintenance program for new equipment as well as scheduled maintenance for existing plant, involves a structured decision-making process based on the consequences of functional failure of this equipment. RCM analysis produces a program which includes all scheduled tasks - and only those tasks - necessary to ensure safety and operating economy. The decision-making logic behind RCM analysis applies to any complex equipment which requires a maintenance support program aimed at maximizing operating reliability at the lowest cost.
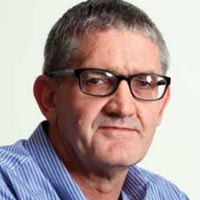
Daan Burger
WearCheck Africa
In this day and age, predictive maintenance and condition monitoring are necessities for any company that has machinery which is critical in achieving production goals. Oil analysis is a condition monitoring technique that has been in use for more than 50 years and has proved to be a highly effective management tool for monitoring the health of lubricated machinery and the lubricants themselves. However, oil analysis is not the only condition monitoring technique available to today"s maintenance professional. Other techniques such as vibration monitoring, thermography and ultra-sonic analysis can also be used. This Technical Bulletin will look at the evolution of maintenance philosophies, the goals of a condition monitoring programme and how a combination of different analytical practices can be used to achieve these goals.
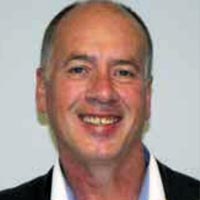
Jan Backer
WearCheck Africa
Maintenance philosophies and practices have been around for many years - the objective of these philosophies being the economic consideration of optimizing plant availability in industry. There has been a steady evolution from breakdown maintenance to predictive maintenance to proactive maintenance in the quest to keep industrial equipment operating economically, efficiently and safely.
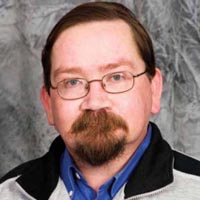